Horological skeleton instruments are an art form that communicate the decorative function of science and time.
A skeleton watch materializes our most intrinsic appreciation of the watchmaking craft. The functional element of the watch is simultaneously the most decorative element. We love watches because the art of making and measuring something is in itself, beautiful. The ability to keep time, to actually have a grasp on the natural forces of the world, is art. A skeleton watch lets this understanding of time speak for itself.
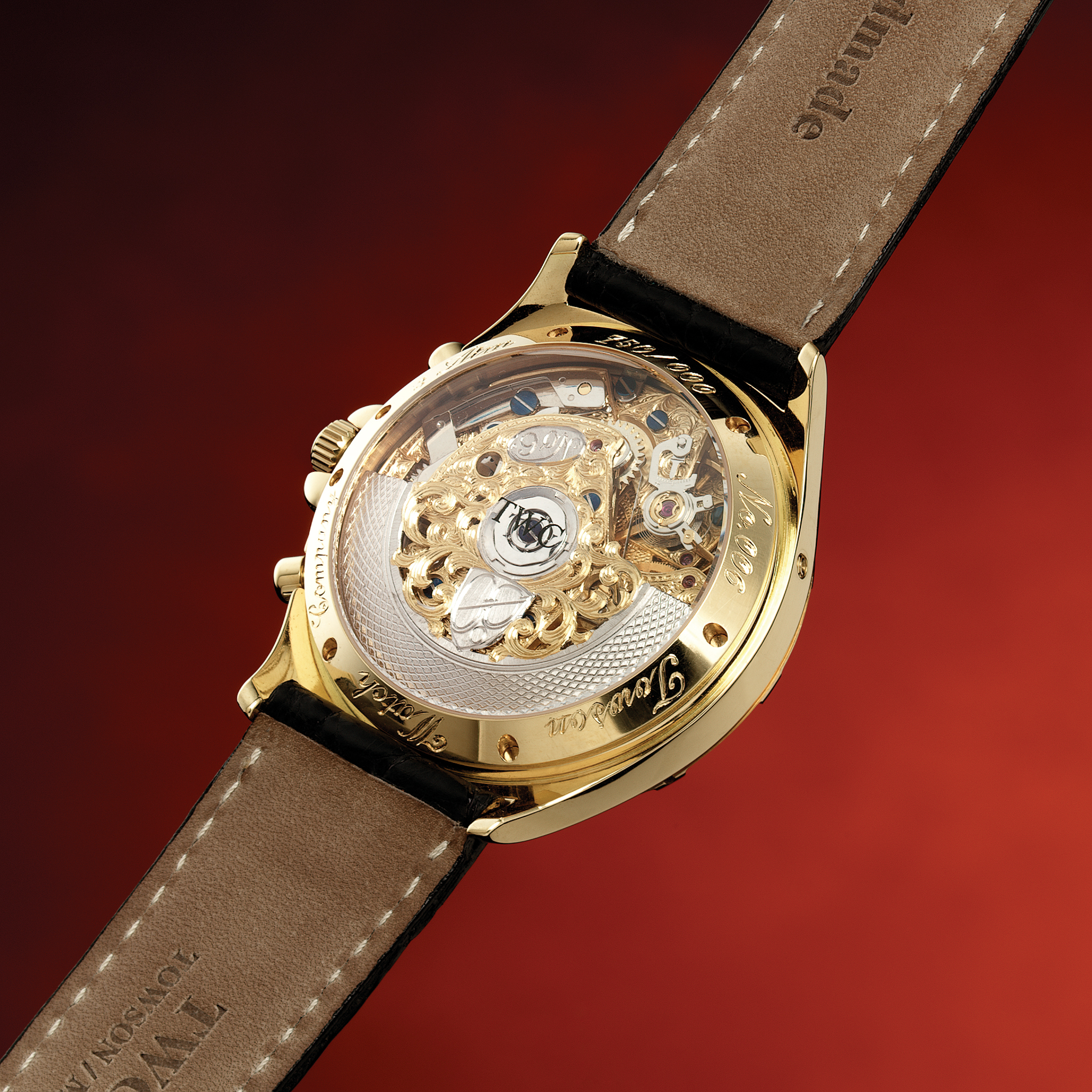
Independent brands like TWC have an advantage when it comes to making timepieces that embrace the artform of our understanding of time. Due to the lack of limitations we endure from mass-distribution and production, we can actually put the time into glorifying the measurement of time with a skeleton watch. Our team of watchmakers experiment with broadened horological ideas for their personal collections just as much as they do design and assembly for the Chesapeake and Mission Collections. This creates an endless realm of creative possibilities for what we can offer in the Master’s Collection.
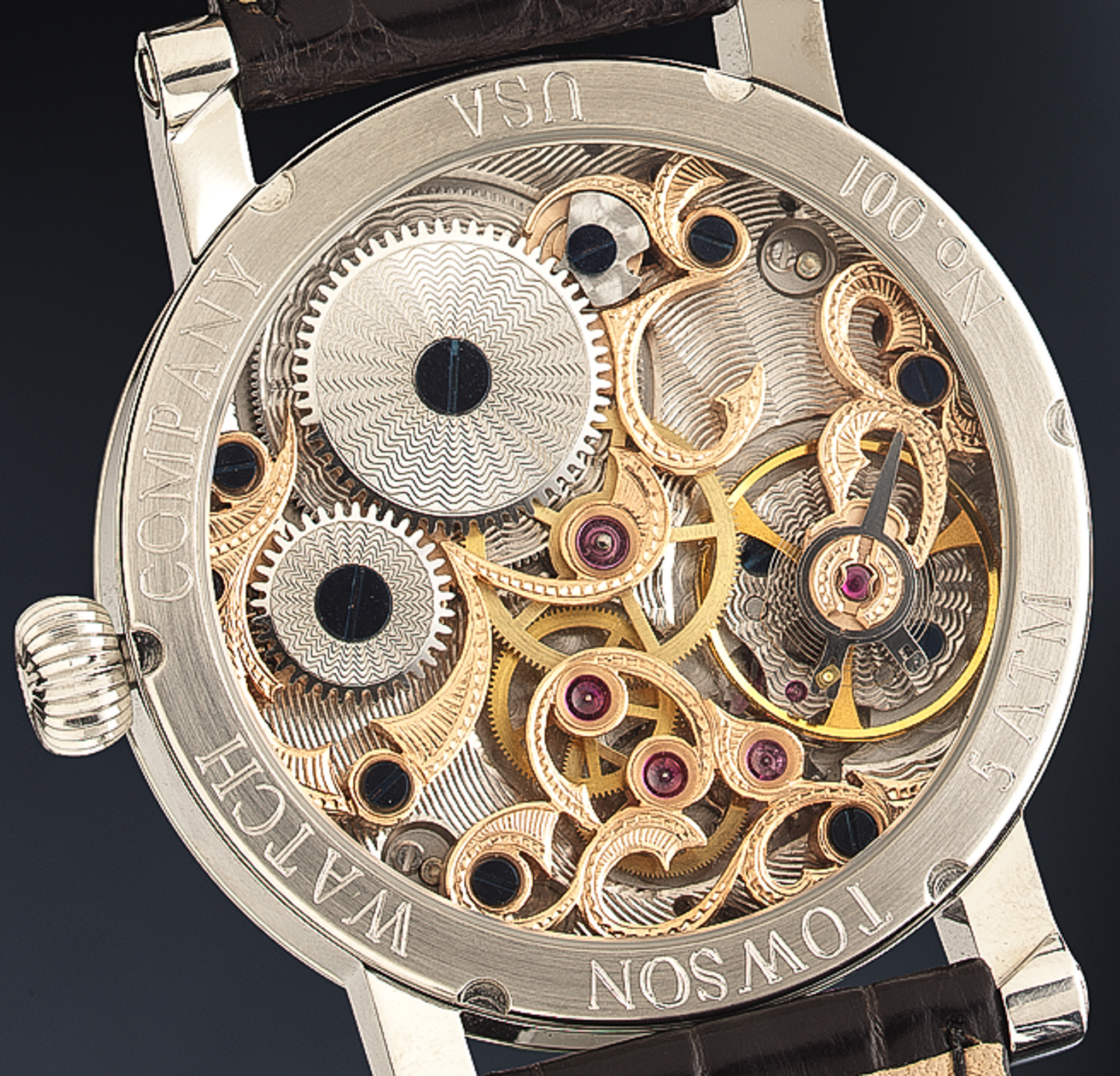
Our watchmakers almost exclusively use vintage tools and machines that they grew up learning on in Germany. This approach to the craft allows for maximum attention to detail and personalization. The 10mm Schaublin and Boley lathes found in the TWC workshop are used to mill small components of the movement with precision. These machine-tools allow us to modify the surface areas of the disassembled Unitas 6498 movement components in order to make the Half Skeleton. The bridges and balance cock must be skeletonized, engraved and plated with gold and rhodium. These alterations lead to several other complications that must be dealt with. The movement is completely turned into something else. Every Half-Skeleton has a different unique interior artwork and is plated in various metals.
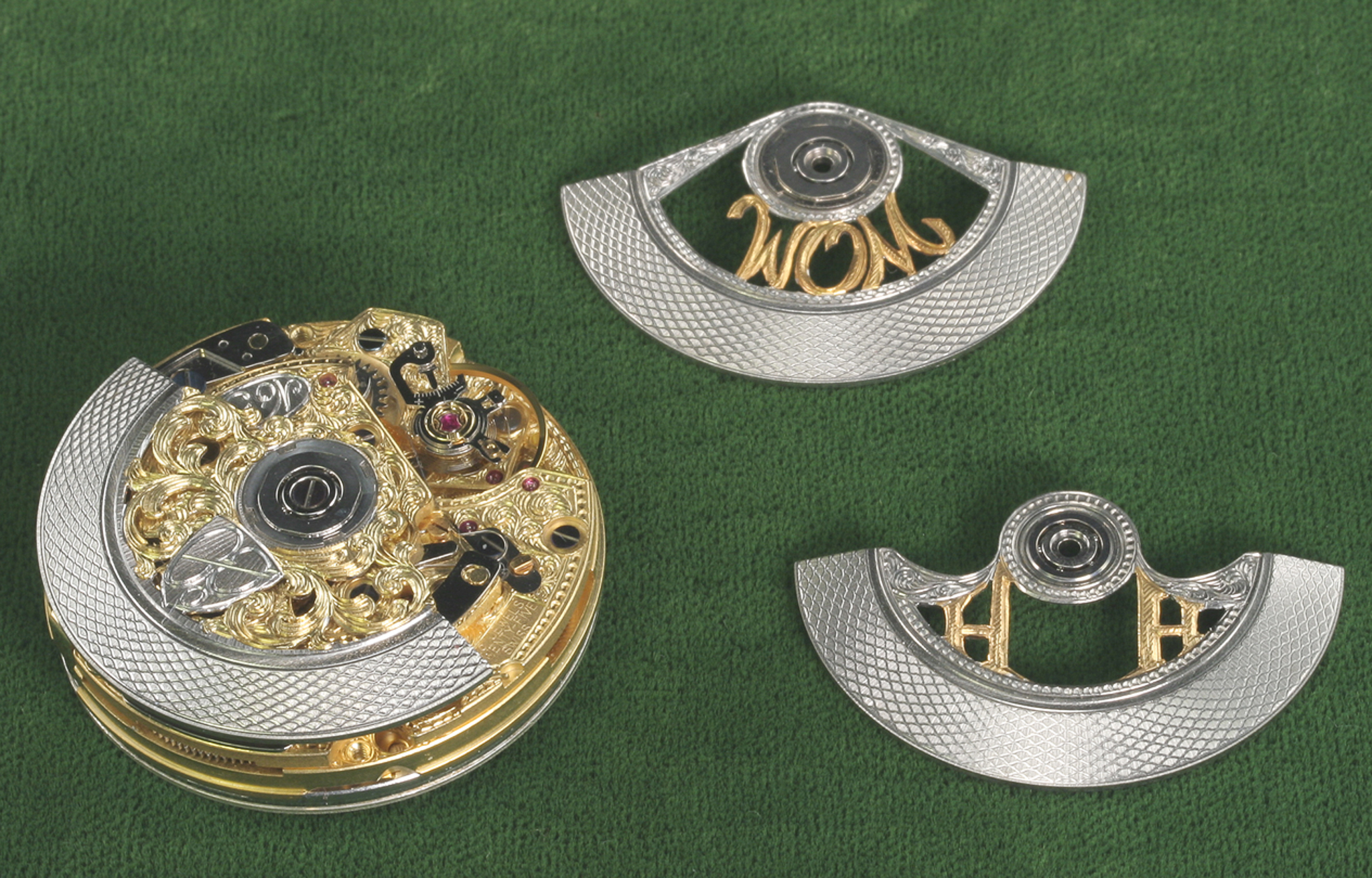
The lathes are also used to manufacture smaller tools that Hartwig makes pinions and staffs with. They allow us to easily make custom fine thread taps from tool steels when repurposing movements.
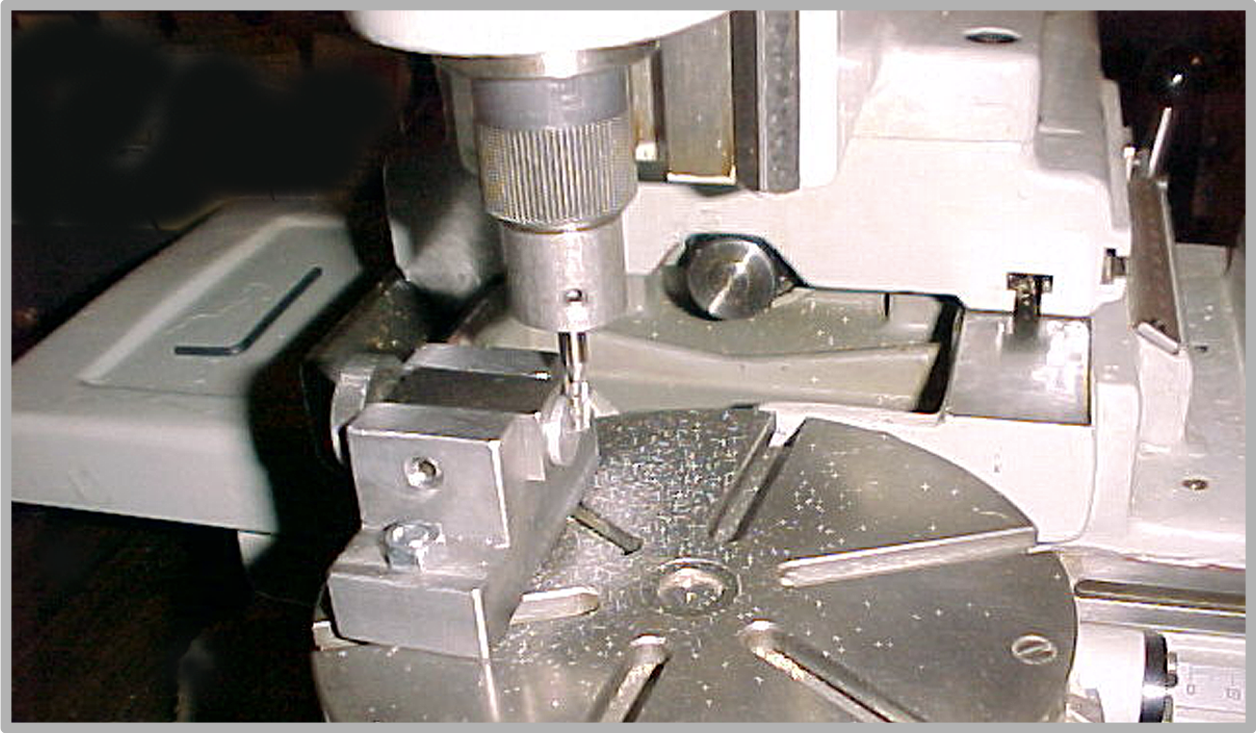
When making a skeleton watch, it’s important to have a complete arsenal of tools. A mini lathe has more mass and power with a trade off of less "feel". It was designed for larger size parts, such as clock parts, and can remove metal faster by taking larger cuts. Also, due to more size, strength and power, a larger lathe will have less deflection from the cutter pressure, thus providing more repeatable accuracy on each cut.
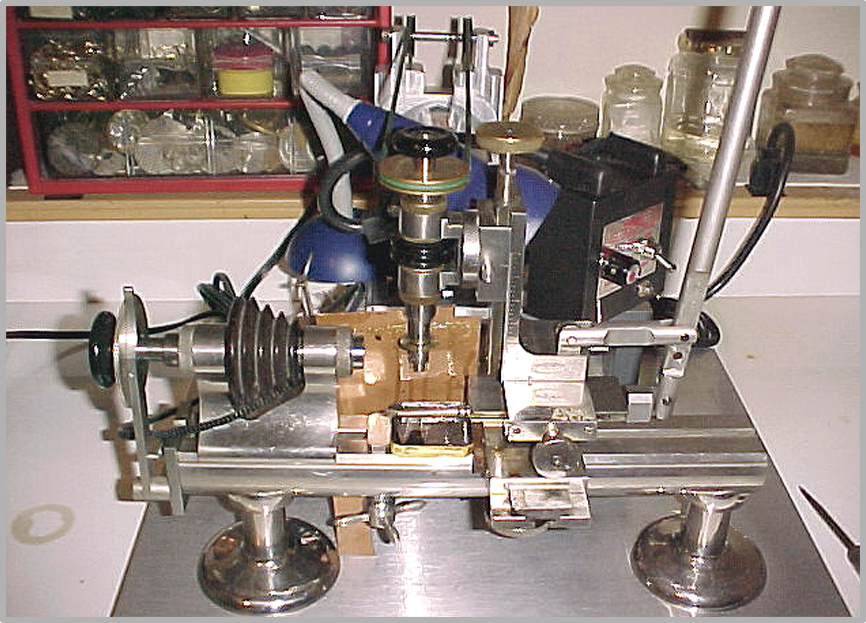
We use the Levin gear cutting machine to make a new click spring. Cold forging makes low carbon steel harder by increasing its molecular density. We use this method to make the spring. The balance cock, foliot (bar-balance), ratchet wheel, counter potence and the wall of the barrels are all hand made from iron using a saw, files, gravers and small pieces of Arkansas stone. The pigs bristle in the regulator, acting as a device to change the amplitude of the foliot’s oscillation, was taken from a good quality paint brush.
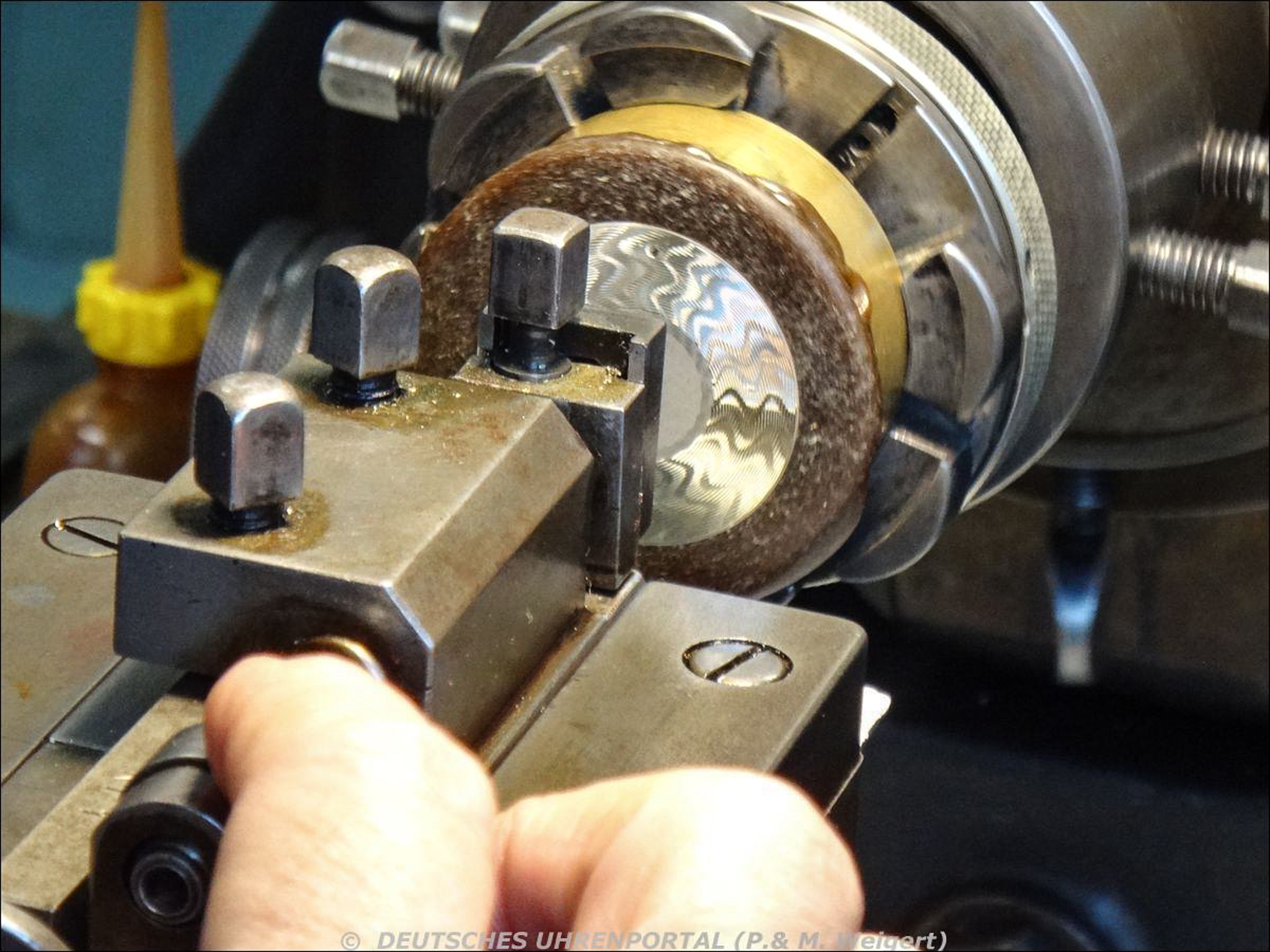
A precision 3 axis milling machine is used to engine turn the 3/4 plate and engrave it with TWC in the small oval field. The balance cock, escape wheel bridge and chronograph bridges are also hand engraved. The pillar plate bears a perlage finish, still left over from the original state of the movement. A new balance was made and installed. A new hour rack was made and installed.
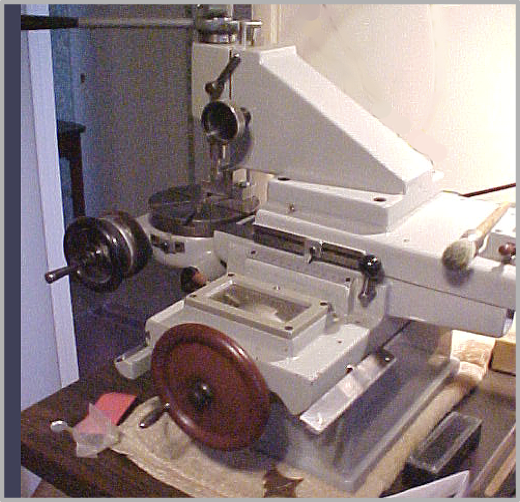
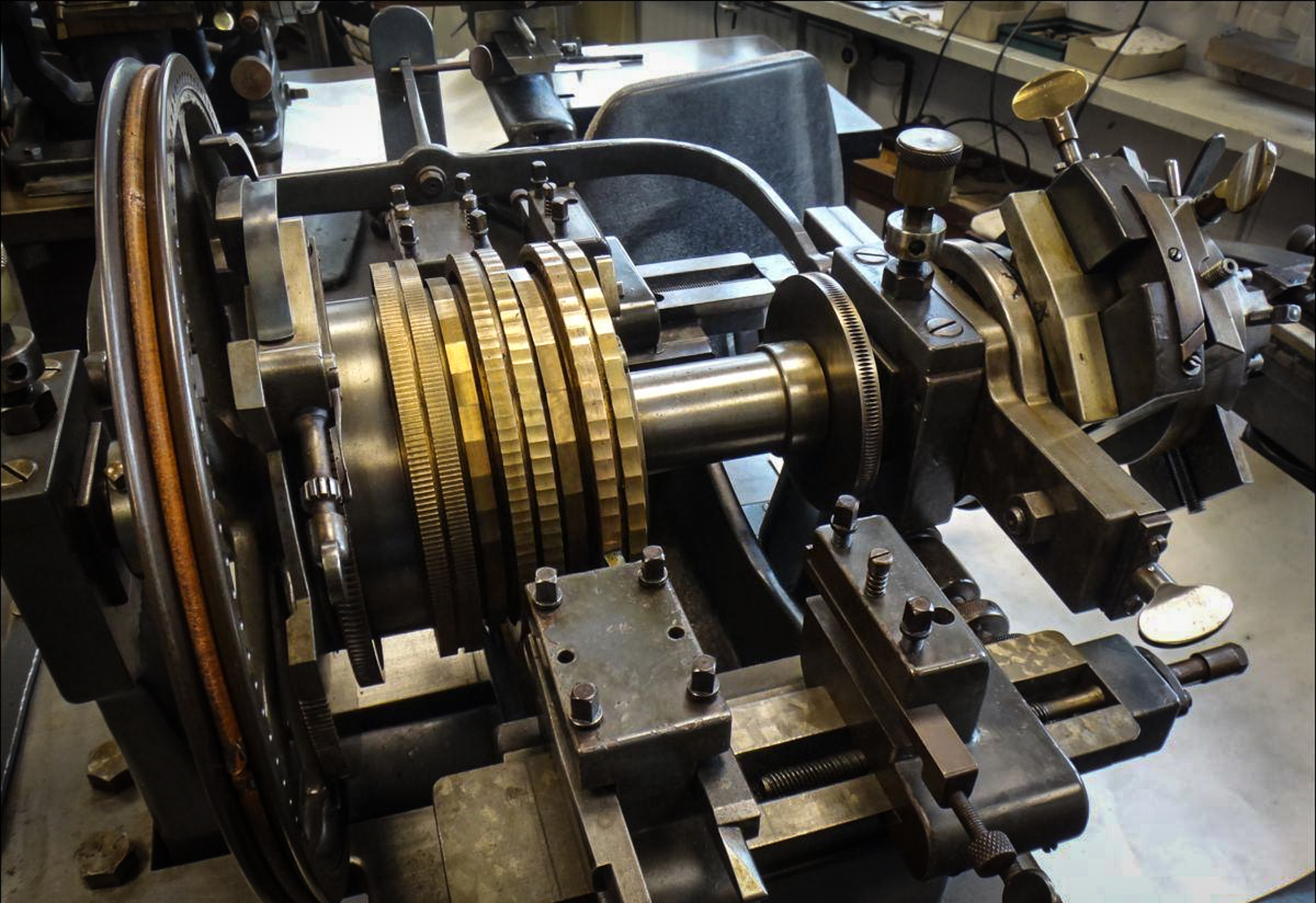
The screwed-on back, securing the case to the center plate, has a sapphire crystal in order to enable the display of the movement. Center plates underside bears the names of all participating artists and craftsmen. The silver dial is engine turned and treated with a heat-application to achieve the frosted effect. We work with our close collaborator in Buenos Aires, Juan Carlos, a silversmith and one of the world’s experts in repousse works.
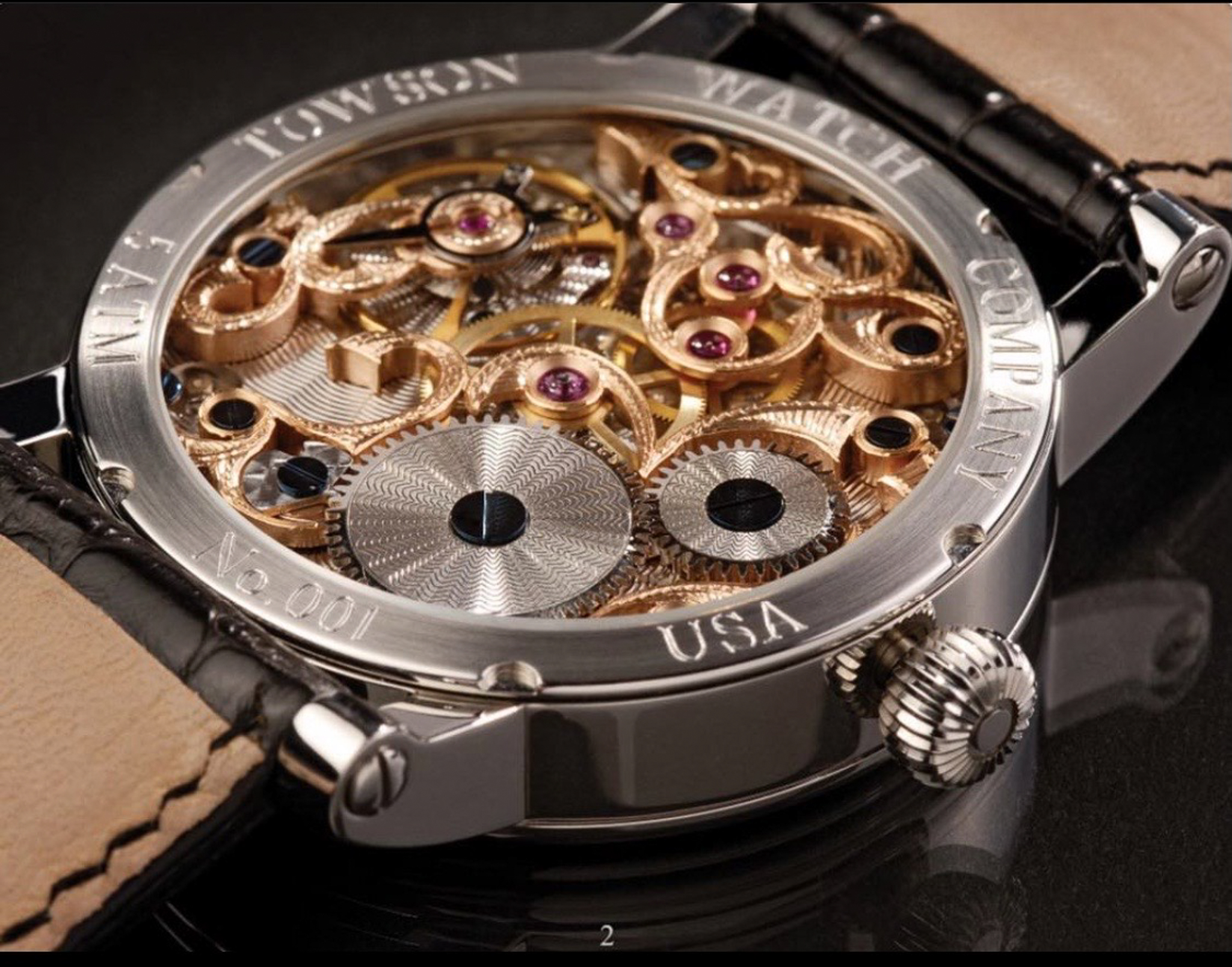
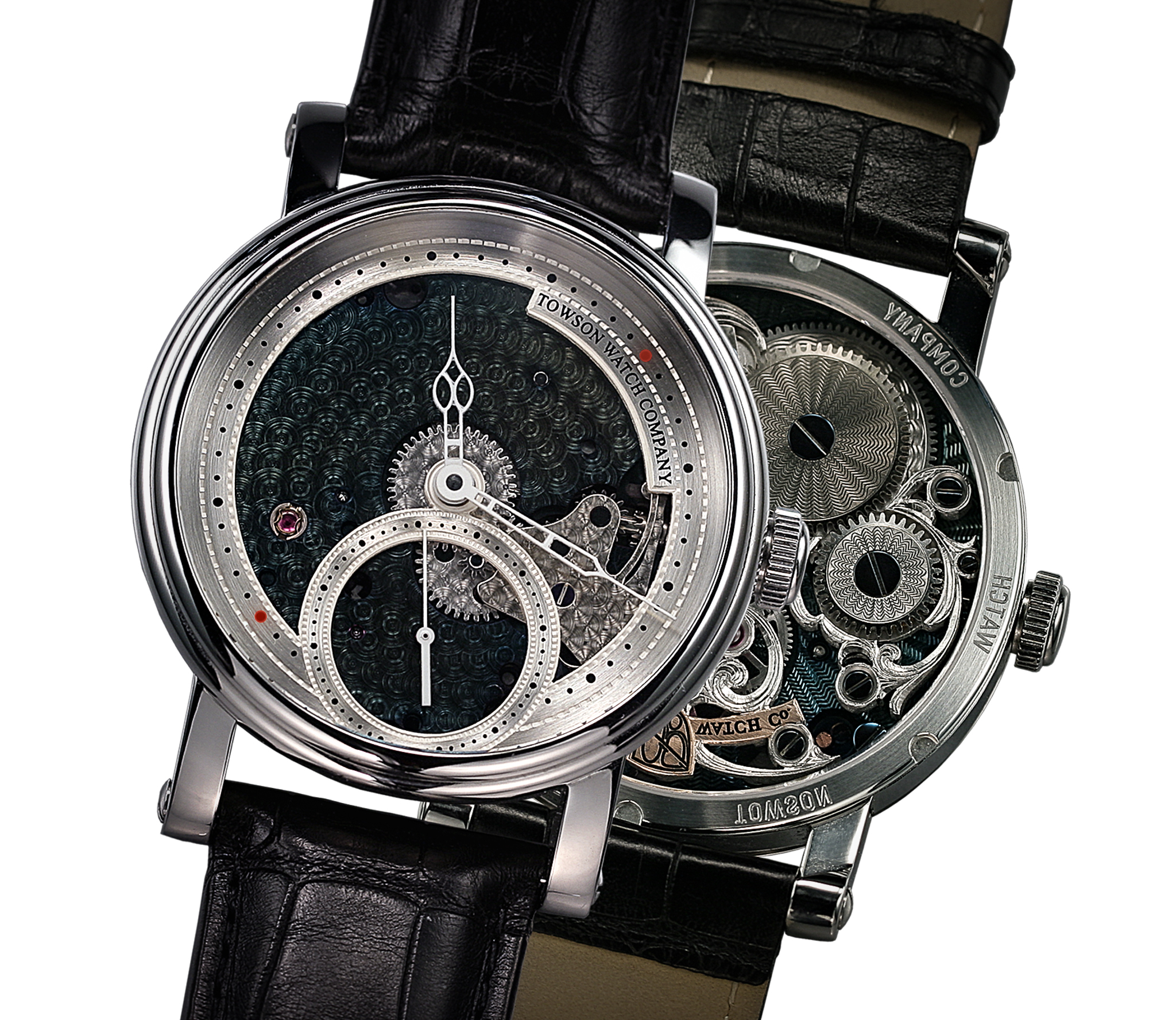
"Horology is the science of time, timekeepers and timekeeping. It is also a category of art, as a horological masterpiece is a representation of the creative vision vested in our understanding of the world. Talent, creativity and vision produce the artistic identity of a horological instrument. To create something special, mechanical instruments of beauty and precision, was always our dream. Our partnership allows us to produce horological works of art, in which George calibrates the time while I craft it."
- Hartwig Balke
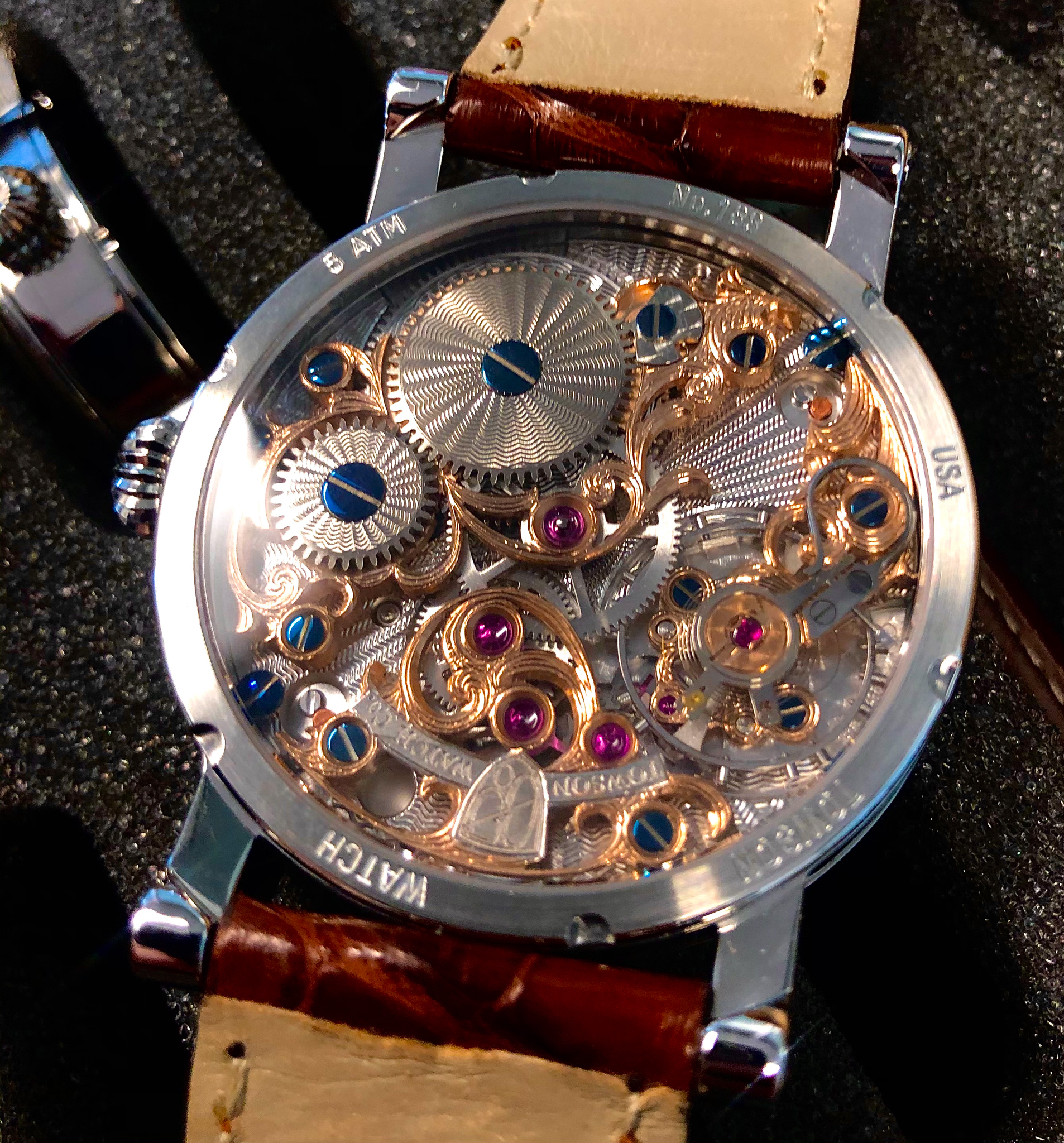